New surface treatment options are now available!
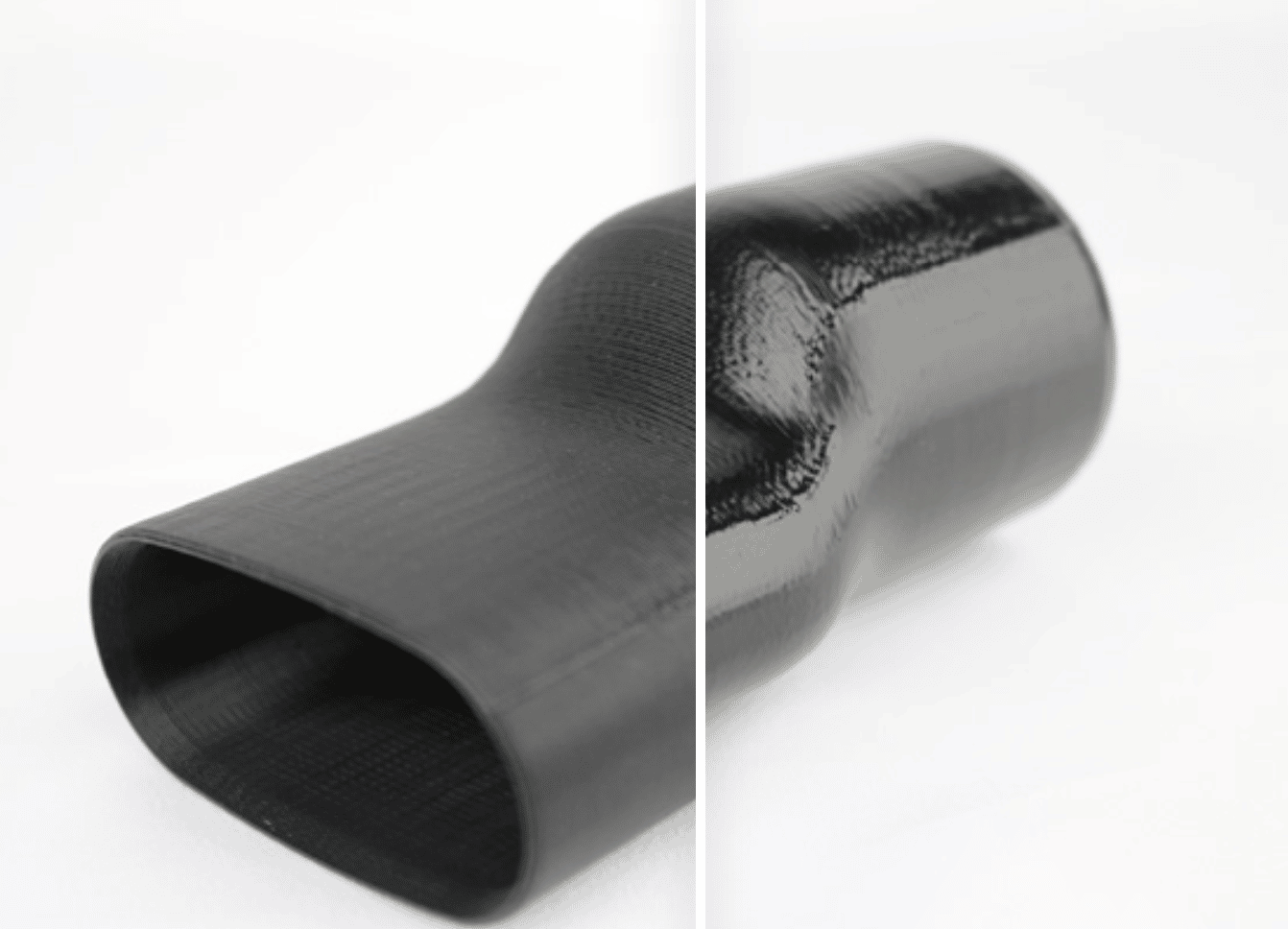
One of the latest additions to our arsenal of machinery here at Fablab Inc allows us to offer a new solvent smoothing option for a large part of our material choices.
Until recently, it was possible to perform this type of solvent smoothing using a common acetone chemical which was applied manually. This only worked for two materials, and the results were less than ideal since the liquid would sometimes pool in some areas, or evaporate too quickly from others. Since this was a labor intensive process, it was difficult to treat larger orders in a uniform, reproducible manner.
We’ve been using this machine regularly since launching the service and and the resulting parts are fantastic. Automating this task is a great advantage to us, and also for our clients, who can now order parts with a finish that resembles what you’d expect from a molded component.
How does it work?
Once your parts are printed, they’re cleaned, trimmed (supports are removed), and prepared in the usual way. They are then carefully arranged in the treatment area and the solvent is applied as a vapor that circulates around and evenly coats all exposed surfaces. We’ve precisely calibrated the machine to be able to handle nearly all the materials we offer with both SLS and FDM technologies.
To learn more about our printing materials click here.
What will this do to my parts?
The end result will be less porous, more even surfaces that show fewer imperfections. These new, glossier surfaces will also have slightly improved mechanical properties, making your part a bit more durable. It’s still possible to tell the difference between parts made with filament or powder based technologies after the process, but the printing lines are greatly reduced with both.
Selective laser sintering, or SLS, produces parts out of powder based materials and they usually have a rough, porous finish. This type of surface is ideal when the parts are meant to be painted or dyed. It’s the best choice in printing technology to make curved, thin, or hollow items since no support material is required. In this case, the surface treatment will melt and re-solidify the outer layer, increasing it’s density slightly since there’s less air.
With filament based parts made by fused material deposition, or FDM, you’ll see the lines and tooling marks greatly reduced. Of course the patterns of filaments will still be visible, but they will protrude less and thin gaps between the lines get filled by the melted material.
To read more about our different printing technologies click here.
Will the dimensions change?
The short answer is yes, but it’s complicated. The volume of the parts won’t change, since the chemical evaporates away, leaving no residue. The reduction issue is caused by the material getting slightly denser at the surface, since those little air pockets and gaps between the layers of filament will be reduced. It’s important to inform our production team of any critical areas where dimensional tolerances are tight, even before printing begins.
To consult our design guide click here.
How much will this cost?
Pricing for this treatment has already been programmed into our website, so you can now select this option from the menus before placing your order. We charge a base price per item that includes handling and also a cost based on the surface area of your part. It’s of course possible to combine items into one batch and obtain a better price, simply let us know when you place your order and we’ll see what savings we can offer.
To use our online calculator click here.