5 important elements to consider when printing in 3D
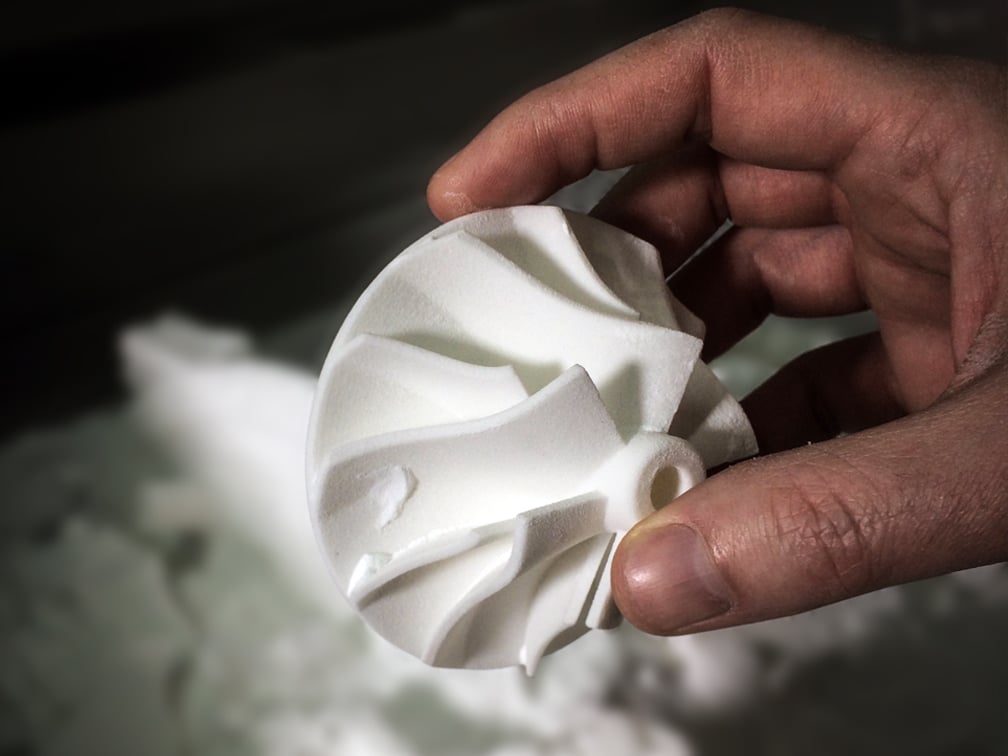
When considering additive manufacturing, there are some important factors to consider regarding the design of the 3D parts. More precisely, these folowing five elements are essential in order to obtain a perfect balance in the creation of your item. The balance between size, resolution, thickness, orientation and choice of material will help ensure the function as well as the aesthetics of your creation.
Size
One feature to consider when creating your item is it’s scale. Each technology has an optimal format, some are larger some smaller.
The FDM machine can reach the largest size, 16 “x 14″ x 16”. If your part is larger than this, it can be sectioned before fabrication and then glued together in a professional manner.
The size of your pieces will have an impact on the fabrication time. Large parts take more time to build and require more material, resulting in higher costs.
The resolution
During additive manufacturing, the resolution refers to the thickness of each layer of material being applied. Depending on the technology used, a thinner layer can reduce imperfections or ridges that might appear on a part’s surface. High resolution allows for a better quality surface and smoother faces before post-processing. The thinner the layers, the more defined the details, and the longer the manufacturing time.
For an object with very high resolution, choose SLA (Stereolitography) technology, which has a layer thickness of up to 25 microns (0.025mm). SLS technology offers very good resolution, i.e. 100 microns (0.1mm). The usual FDM layer thickness is 250 microns (0.25mm) and we also offer high resolution (0.175mm). It’s possible to print in even lower resolution (330 microns, 0.330mm). This happens to be a good option for larger, less aesthetic objects, manufactured quickly and at a lower cost.
Wall thickness
The thickness of the component’s walls is a fundamental characteristic of your design which ensures stability, precision and tolerance for an additive manufacturing part. Smaller thickness shortens build time, but too thin can result in a brittle part with less precise characteristics.
Thin parts built with SLS are more likely to warp due to the the manufacturing process. Pieces made by the SLS method are subject to high temperatures as well as the weight of the powder during manufacture. The material used in SLS can also shrink as it cools and solidifies. With a thickness between 1mm and 3mm, a geometric stability of these characteristics is more easily achieved. It’s still possible to achieve a minimum thickness of 0.4mm. This is however riskier.
With FDM, for example, the recommended minimum thickness is typically 1.6mm
The orientation
In 3D printing, the orientation refers to how the part is placed on the print platform. It can be oriented at an angle, lay flat, or placed vertically. Orienting the components correctly for fabrication is a critical step that affects the final quality, especially when it comes to geometric dimension and error tolerance. The energy used and the extent of support structures required are also directly affected. All these factors contribute to the total cost of the part.
Orientation may also vary depending on the technology being used. With FDM, the printed part has a very high elastic force on the X-Y axis but exhibits more weakness on the Z direction due to the way the layers are printed. Poor preparation at this level can make the lines between each layer visible, affecting the aesthetics of your parts. For this reason, certain orientations are preferred for curved shapes. In some cases, the orientations will be more effective if they overhang the surface, thus requiring more support.
This being said, we will take care of positioning your parts so that they have the best ratio between surface quality and part strength, unless otherwise specified.
The choice of material
Depending on the method you select, there are different materials to chose for your 3D print. Your choice is typically made according to the constraints that apply to your component. If your part must have particular resistances, it is important to be selective in your material choice. For example, if it will be subjected to very high temperatures, or chemical solvents, you should consider ULTEM (in FDM technology). If it needs to be impact resistant, polycarbonate will be a good choice.
SLA technology also offers interesting resins for various applications. If you want a material that has properties similar to rubber, try selecting flexible resin. If you want to make a lost wax casting, we have “castable wax” resin available. On the other hand, if you just want to have the object in hand without a particular use, ABS (FDM), Nylon (SLS) and acrylic resin (SLA) will do the job very well at a reasonable cost.
Design balance
The size, resolution, thickness, orientation and choice of material are all important elements of a creation dedicated to 3D printing.When these factors are all considered and balanced, you are sure to get a functional part that meets your needs.