3D Printing technologies
Our different 3D printing technologies
3D printing is an additive manufacturing technique developed for rapid prototyping. The essential process remains the same for most methods, where adding layer after layer of material builds your parts. However, the technologies use different processes, material choices, and operations to offer a wide range of options. 3D printing allows unique parts to be fabricated while avoiding conventional production techniques. Here are the available technologies we offer to realize your projects.
Plastic Powder (SLS)
SLS technology has multiple advantages compared to other printing methods. It prints parts using durable materials, offers a reliable level detail and the prices are often the lowest you can find. Selective laser sintering is the best option for curved and hollow shapes, since no support material is required. It’s therefore very easy to clean and prepare the parts after printing.
Plastic Filament (FDM)
FDM technology is ideal for direct digital manufacturing (DDM) of final prototypes or for small series of parts that are used with finished products. It makes additive manufacturing of functional parts possible by using deposits of extruded thermoplastic polymer layers such as ABS or polycarbonate.
Plastic Resin (SLA & Polyjet)
We use a process of high definition super fast stereolithography (SLA) which allows us to make objects within a few hours. We can produce molds for casting, models for functional testing or presentations in high quality and at reasonable prices.
Polyjet technology is similar to SLA, but can achieve a finer level of detail. It’s even possible to combine materials.
Metal Powder (DMLS)
DMLS technology lets you build your concept models directly out of metal. It’s ideal for making prototypes and functional parts that need good mechanical properties. Parts made by direct metal laser sintering are durable and can be machined and polished with ease.
Plastic Powder (SLS)
Selective Laser Sintering
Selective laser sintering is an advanced 3D printing technology advanced that can create parts from powder material. The powder is fused layer by layer by a laser. It is then possible to manufacture precise parts, using high-performance materials such as nylon. Moreover, the lack of support material used to produce parts makes it cheaper. This technology can be used in all areas, from toys to aircraft parts.
- Functional parts and finished products
- Complex and detailed designs
- Moving parts or assemblies
- Possible to dye the parts any color
Selective Laser Sintering
Dimensions
- Printing volume : 13 x 11 x 16 inches (33 x 28 x 40 cm)
- Minimum wall thickness : 0.03 inches (0.762 mm)
- Minimum detail size : 0.02 inches (0.508 mm)
- Minimum protruding/engraved feature : 0.025 inches (0.635 mm)
- Minimum hole diameter : 0.039 inches (0.9906 mm)
Other Details
- Layer thickness: 0.1mm.
- Good reproducibility of identical parts
- Strong and resistant materials
- Allows small details such as text and watermarks
Selective Laser Sintering
SLS vs FDM
- Better surface finish
- Uniform mechanical properties in each direction
- Needs little to no finishing after printing
- No support material is required
SLS vs SLA
- Stronger materials
- Can produce interlocked objects or assemblies
- Also doesn’t need support material to be added
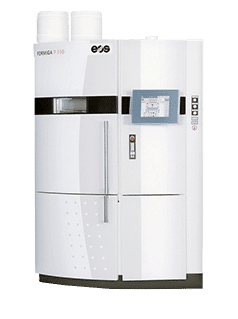
Plastic Filament (FDM)
Fused Deposition Modeling
This technique consists in melting a thermoplatic resin through a hot nozzle similar as a glue gun. The machine then drops layers by layers a micro thread of melted thermoplastic all along the way traced by computer.We consider every aspects of mechanical, esthetic or functional resistance when we estimate every parts to make sure you have the best quality for your money.
- Excellent mechanical strength to make assembly tests under real conditions
- Long-lasting thermoplastics
- Excellent thermal resistance: 95 ° C to 138 ° C
- Very good dimensional accuracy
- Ideal for direct digital manufacturing (DDM) in large quantities of small parts
Production delay : 1 working day (minimum)
Fused Deposition Modeling
Dimensions
- Printing volume : 16 x 16 x 14 inches (40.6 x 40.6 x 35.6 cm)
- Minimum wall thickness : 0.03 inches (0.762 mm)
- Minimum detail size : 0.02 inches (0.508 mm)
- Minimum protruding/engraved feature : 0.025 inches (0.635 mm)
- Minimum hole diameter : 0.039 inches (0.9906 mm)
Other Details
- Thickness of standard layer : 0.010″
- Thickness of high resolution layer : 0.005″ – Precision : +/- 0.005″ first 5 inches, then +/- 0.0015″ by inches added (ABS)*
- Reproducibility of identical part (ABS) +/- .001″
- Finish : visible construction layers (height depends on resolution)
* depending on the geometry
Fused Deposition Modeling
FDM vs SLA
- Material used with FDM are long-lasting thermoplastics : they do not worsen with time and UV.
- Best thermal resistance.
- Parts made with FDM have better dimensional precision and better reproductibility.
FDM vs Polyjet
- Larger parts
- Assemblied parts more resistant : parts made with FDM hold well together.
- Best thermal resistance
- Compatible with RF signals (Polyjet is not compatible with RF signals).
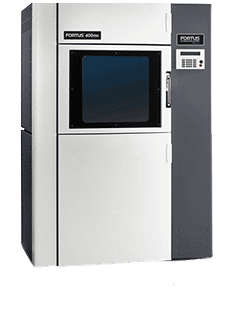
Plastic Resin (SLA & Polyjet)
Stereolitography (SL or SLA)
Stereolitography is a prototyping technic that allows to manufacture objects from photopolymer. Polymerization is induced by a laser light that scans layer by layer the resin tank until the part is completed. It is possible to get very precised parts in no time.
- Very rapid process
- Impressive details finite : ideal for casting templates
- Economic for identical parts series.
Polyjet
Another option that uses resin is Polyjet technology. In this case, the resin is deposited layer by layer by an inkjet like printer head that can be fed with a range of materials. This is the most accurate printing technology, making it able to produce thin, complex geometries.
Contact us for more details.
Stereolitography (SL or SLA)
Dimensions
- Printing volume : 5.7 x 6.8 x 5.7 inches (14.5 x 17.5 x 14.5 cm)
- Minimum wall thickness : 0.03 inches (0.762 mm)
- Minimum detail size : 0.025 inches (0.635 mm)
- Minimum protruding/engraved feature : 0.025 inches (0.635 mm)
- Minimum hole diameter : 0.03 inches (0.762 mm)
Other Details
- Low resolution layer thickness (HD4): 0.004 inches (0.1 mm)
- Standard resolution layer thickness (HD2): 0.002 inches (0.05 mm)
- High resolution layer thickness (HD1): 0.001inches (0.025 mm)
- Finish : little to no visible construction layers.
Polyjet
Dimensions
- Printing volume : 9.8 x 5.9 x 9.8 inches (25 x 15 x 25 cm)
- Minimum wall thickness : 0.024 inches (0.6096 mm)
- Minimum detail size : 0.008 inches (0.2032 mm)
- Minimum protruding/engraved feature : 0.025 inches (0.635 mm)
- Minimum hole diameter : 0.01 inches (0.254 mm)
Contact us for more details.
Stereolitography (SL or SLA)
SLA vs FDM
- Faster production
- Same strenght in all the axis
- Little to no finishing
- Fine details
- Tight parts (Waterproof parts)
SLA vs SLS
- Smoother surface finish
- Transparent materials
Polyjet
Contact us for more details.
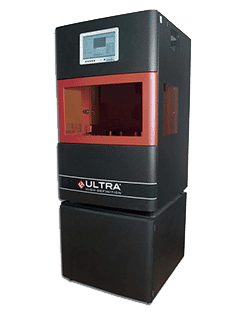
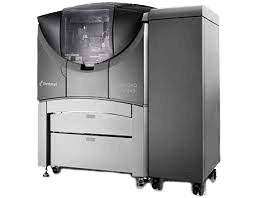
Metal Powder (DMLS)
Direct Metal Laser Sintering
This is an additive manufacturing technology that uses a variety of metal alloys in powdered form. Allowing prototypes to be made from the same material as final production components. Same as with SLS technology, DMLS parts are built layer by layer from a metallic powder that is solidified by a laser. The technique makes it possible to design complex geometries while integrating internal features such hollow sections and ducts, which would otherwise be machined. DMLS technology produces strong and durable metal components that can be used as functional parts.
- Functional components made directly out of metal
- Strong and durable parts
- Metal alloys
- Freedom of design versus standard production means
Direct Metal Laser Sintering
Dimensions
- Printing volume : 11.8 x 11.8 x 11.8 inches (30 x 30 x 30 cm)
- Minimum wall thickness : 0.012 inches (0.3048 mm)
- Minimum detail size : 0.015 inches (0.381 mm)
- Minimum protruding/engraved feature : 0.025 inches (0.635 mm)
- Minimum hole diameter : 0.02 inches (0.508 mm)
Other Details
- Layer thickness : 0.1mm
- Finish: slightly porous
- Parts are easy to machine and polish
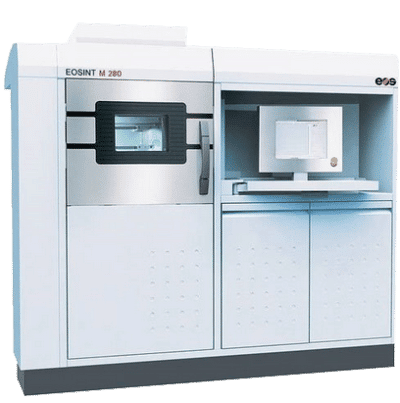